A story of transitioning from a slow, dilapidated, development environment to a lean innovation engine.
I joined the company as a manager in the mechanical engineering department in 2011. We had a waterfall product development system. I recall one project that had been in process for 12-months when I arrived. I worked with the mechanical design team for the next 6-months and saw obvious signs of frustration; micromanagement from the executive level; continuous requirements modifications; no collaboration with operations or suppliers. Eighteen months into the project the scope was dramatically changed due to market corrections, resting the project on another 12-month+ runway. Two months later, the project was cancelled. Twenty months with nothing to show for it. How depressing.
My first week on the job, I attended an “all-hands” meeting with engineering where engineering management rolled our 5-page, laminated flip chart of the “design review checklist” matrix. Each page represented a project phase. Each page included a matrix of engineering disciples and the required reviews based on design subject or complexity. It was very thoroughly thought out by management. Clearly, they spent hours over several months thinking about every aspect of design. I’m sure they thought this was a brilliant, fault-proof tool. No design error would escape this labyrinth!
As a mechanical engineering manager, I was expected to implement this policy. As I met with my team and we tried to follow the path laid out for us, we immediately ran into blockages. Who do we meet with to satisfy this box? How do we achieve that criterion? What seemed obvious to “management” was not at all clear to the engineers. Solution: meetings! Meet with management to get clarification. Meet with team members to follow management guidance. Meet with management to follow-up on team member questions on management guidance. Meet with team on management team member guidance from management guidance meeting… Got it. Prepare for the design review! Slides. Images. Pre-meeting review. Update slides. Now we are ready. Feasibility design review of concept with executive level. They don’t like it. Take feedback, redesign. Meetings, review, guidance, re-review, design… you get the picture. This was clearly not working. Why is the project overrunning the schedule and budget. Meeting! Lessons learned. Geez, this is frustrating just writing about it! Don’t worry, it has a happy ending.
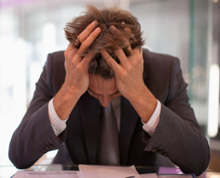
Enter, new engineering VP. He had the same observations above over the next 12-months. And apparently, so did the quality and the operations VP! Together they embarked on a mission to find a better way. That way was found at LPPDE in North Carolina in 2014. At the Monday workshops, they learned about Lean Product and Process Development and these simple, logical principles.
- Entrepreneurial System Designer
- Teams of Responsible Experts
- Cadence Pull and Flow
- Set Based Innovation
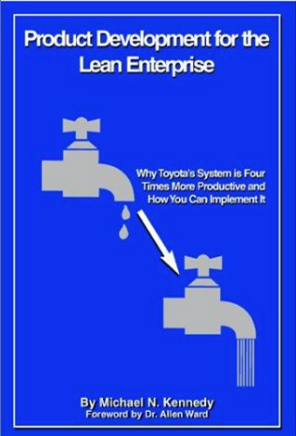
They also picked up some key books such as Product Development for the Lean Enterprise, by Michael Kennedy and Lean Product and Process Development, by Allen Ward and Durward Sobek. These books became required reading for the management teams. In parallel, we began regular (cadenced) meetings with the management staff and key champions about whether these principles could help us. If so, how can we start implementing them? It was immediately clear that this was much better than what we had and that we could start practicing these principles immediately.
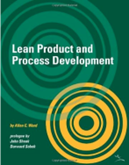
Success was assured and it has endured.
One of the first initiatives was to convert our Systems Engineers to Entrepreneurial Systems Designers (Chief Engineers). What’s the difference between SE and CE? The Chief has full responsibility for the success of their product line. The system engineer was only responsible for the requirements and the validation of those requirements. Success! The teams were excited. Finally, someone close to the team was “responsible” for its success. Not the executive class.
Finally, it was time to put it all together on a new product development project. The new product was a transmittion detection system for our mobile backscatter product. The challenge we were faced with was that cars would need to drive over the detector, and we had never attempted this before. The detector had to:
- Not move
- Not get crushed
- Minimize impact on the x-ray image
This was our first opportunity to implement Set-Based Innovation. In the past, we would have spent months on concepts and analysis and detailed design, then build this grand prototype with all the hope in the world that it would work. Why wouldn’t it? We had 11 design reviews with all the VPs! No. We rapidly conceptualized 4 different ramps (to protect the detectors). We made it a bit of a competition with different engineers trying different approaches. These prototypes were bought with minimal engineering documentation from suppliers we could collaborate with in order to get us prototypes fast and that were “good enough” to represent the concept. Finally, we tested them all and measured the parameters listed above on all of them. We tested on hills, in the rain, in the snow and with car, trucks and trailers. In the end, we plotted the performance. Then, including ease of use and cost, we selected our design. In the 12 years of production since, we have not deviated from that chosen design. Success was assured and it has endured.
So what was the key to this transformation? Yes, we had VP level support. But I think the key was courage. The courage to try something new. The courage to fail. The humility to know you may be the sources of failure. But by facing these fears, we were able to break from the slow, stagnant process we had devolved into. By facing these challenges, we inspired an entire department and beyond that, the whole operational team as we embraced Purchasing and Manufacturing in Design-for-Manufacturing and Design-to-Cost and more. Through courage and perseverance, we transformed into a lean, enthusiastic team, ready to move fast and succeed.
Questions;
Do you agree with how these methodologies are characterized?
What methodology does your organization of visual communitcation?
Join the conversation at our LinkIn group!
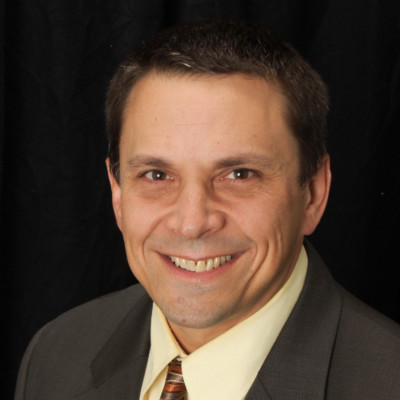
Geoff Neiley
Director CPI and CM, Rapiscan Systems
Geoff Neiley has been in the mechanical engineering field for 30 years. After graduating from the University of Maine, Orono, he learned much about the custom equipment business at NESLAB Instruments designing water chilling systems. Following this he spent 15 years working for BTU International where he designed and lead projects for conveyorized furnaces using in the electronics and solar industry. During this time, he earned his master’s in mechanical engineering at the University of Massachusetts, Lowell. It was at BTU where Geoff began to see the value of concurrent engineering. Geoff joined AS&E in 2011 where he led the mechanical team to introduce state-or-the-art x-ray products for the security market. Three years after joining AS&E (now Rapiscan Systems) in 2011, the leadership team introduced the concept of Lean Product Development. Geoff joined the leadership team reading many Lean PD books, inviting Lead PD practitioners to AS&E and attending LPPDE for several consecutive years. AS&E has roundly embraced the concurrent engineering aspects of Lean PD focusing greatly of Set-Base Innovation and cross-functional collaboration with our supply chain and manufacturing team. In 2022, Geoff took the role of Director of Continuous Product Improvement and Configuration Management. In his new role, he continues to leverage his learning from 8-years for practicing LPPD. Geoff has been a member of the board of Lean Product and Process Development Exchange since 2019. Today he is still learning and experimenting with lean processes and enjoys the pride felt in enabling a cross-functional team to achieve challenging, rewarding goals.