I will be at the LPPD Exchange Munich Conference (April 2023) (Link to full agenda) and am excited to share why implementing lean sometimes is so hard.
Having practiced Lean for more than 15 years in different industries, countries and environments, it still strikes me how something that should be so easy and based on common sense can be so hard.
At the conference, we will talk about one of the most common mistakes in implementing Lean is that we take the copy paste approach where the methodology is taken out of its context and applied in a different one. When what we should be doing is making sure we understand the problem we are trying to fix, the principles behind the method that can help us to solve the problem and then adapt the method so that it fits into the environment where we are trying to apply it. Having been in the vehicle production industry I have seen this multiple times when methods and tools are being lifted from a production environment into a service or admin environment – very seldom is this a success story.
Lean cannot be implemented as a standalone structure
Furthermore, when a Lean effort has reached a certain success and maturity the ambition might be to raise the bar and develop Lean into an enterprise system in order to eventually reach a cultural shift. When we get this far in our Lean journey there is another important factor to be aware of. Lean (in my opinion) cannot be implemented as a standalone structure – it needs to be integrated into existing structures. If Lean is added as something on the side, there will be a lot of energy wasted on internal competition and struggles between stakeholders.
As Lean practitioners we need to be able to analyze the complete system of a business and organization in order to discern what parts that are working well, not so well and what parts need to be put into place. Based on a thorough analysis of existing structures we can make a plan to fix what is broken, add what is needed and leave the things alone that are working well. The last part is the most important one – do not fix what is not broken!
During my session at the, LPPDE Munich conference (April 2023), I will share some failures and learnings on this topic and hope to inspire a great discussion. I hope to see you there.
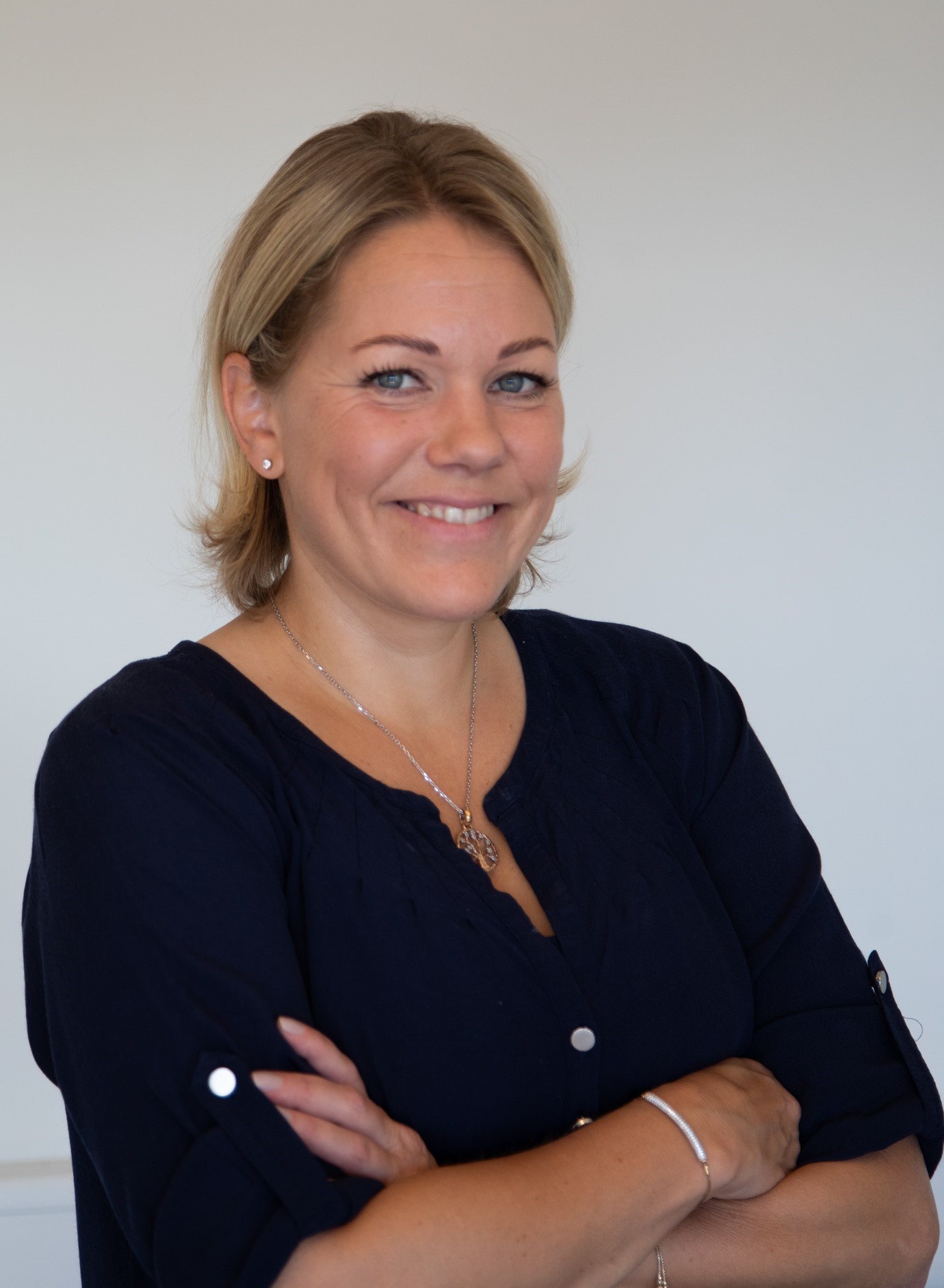
Ingela Hofverberg
Chief Transformation and Quality Officer
Ingela is currently Chief Transformation and Quality Officer at a company within the Lifescience industry. She is a highly experienced, driven, and passionate leader with more than 15 years of working with business transformation. Ingela has designed and implemented management systems and structures founded on Lean principles and values.
Upcoming Event: LPPDE Europe 2023 In-Person Conference
April 24-26, 2023 in Munich, Germany
Extreme Ownership
Join some of the leading practitioners in Lean Agile Digitalization and Leadership who will share, how digitization combined with servant leaders and trusted teams taking "Extreme Ownership", plays out to support teams to learn and decide quickly, and win on any challenge to satisfy their customers.
See updates to the program at LPPDE EU 2023.