A few years ago, at LPPDE NA, I sat at a discussion table with Jim Morgan. The subject at this table was the Chief Engineering role in an organization. He shared that as a chief engineer at Ford he wanted to build “Towering Technical Competency” in the engineering disciplines. I was inspired by this idea. It goes beyond just having “good” engineers or “good” engineering. It relates to a personal, unselfish desire to make everyone in the group great! That, together, we can be a technical force for the organization – that you can make me better, and I can make you better, and together we will be a great engineering group providing great designs to the organization. That we will support our peer disciplines and they will enhance us. He described a cadenced design review within the teams where team members shared their new and old knowledge. Where team members bring challenges to their peers for help and bring new knowledge to inspire others. An intentional forum for collaborative sharing and learning.
No Preparation Allowed
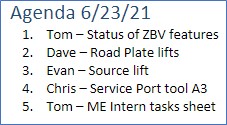
I brought the idea of cadenced design reviews to my team shortly after and we have been conducting these sessions for the past several years. We meet every two weeks, and we call it “Show and Tell”. I encourage team members to bring challenges they are facing, processes they have learned or created, and technologies they have discovered. I listen between events for topics that I think the team would appreciate and record them in a public agenda area. Others are welcome to add to the agenda as they identify topics for sharing. As the months and years have passed, the enthusiasm for sharing has continued to grow. Team members look forward to Show and Tell as an opportunity to teach what they have learned, and for what they may learn at the next meeting.
One key aspect of Show and Tell is “No preparation allowed”! Team members are not to spend time creating slide show presentations. They must only share the work product that they are producing for their project. I encourage all work to be done on an A3 from the current situation through countermeasures. At any point in the lifecycle of an A3, team members can gain or impart knowledge to the team. Feedback from teammates enhances the value in the A3. And knowledge on the A3 informs team members during the discussion. When the effort is at an end, the A3 stands as a record of knowledge gained. If you don’t have an A3, or if the knowledge to be shared needs more detail, an engineer may share a CAD model in the native tool. Maybe they are demonstrating a new CAD technique they discovered. Maybe it is an excel calculation spreadsheet for calculating bolt clearances or thermal loads. Or maybe it is a video on an ingenious mechanism someone thought was “cool”. Whatever they have to share is a learning opportunity for all.
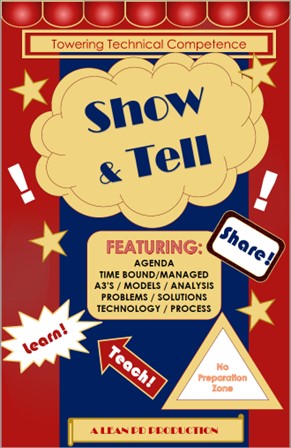
Finally, how do we retain the knowledge shared? We use a simple, ‘rough’ knowledge storage system. For us, it is a Microsoft Teams directory a tool already widely used in our organization. The Teams interface allows for storing in relevant folders. But more powerful is the search tool. We can search keywords throughout documents to find prior knowledge. But in addition to the knowledge shareing database, we are imprinting memories into team members. Some may recall that Dan did a calculator for bolts. Where did he put that? Didn’t Dave show something on lifting heavy devices a year ago? Let’s look in the KSD for an A3. The personal, human aspect of sharing and collaborating stays with us and helps us retain learned competency.
Are you building Towering Technical Competency in your department or organization? Do you have other techniques for spreading knowledge throughout your teams? I would love to hear your feedback.
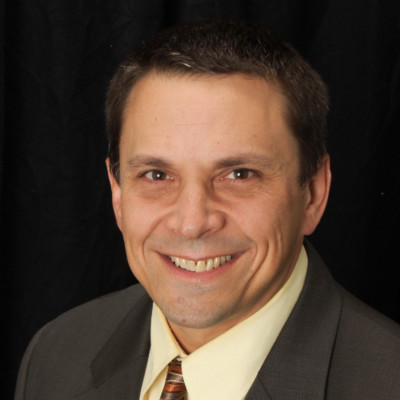
Geoff Neiley
Geoff Neiley has been in the mechanical engineering field for 25 years. He spent 15 years working for BTU International where he designed and lead projects for conveyorized furnaces using in the electronics and solar industry. It was at BTU where Geoff began to see the reap the values of concurrent engineering. 3 years after joining AS&E in 2011, the leadership team introduced the concept of Lean Product Development. Geoff joined the leadership team reading many Lean PD books, inviting Lead PD practitioners to AS&E and attending LPPDE for several consecutive years. Today he is still learning and experimenting with lean processes and enjoys the pride felt in team by enabling cross-functional to achieve challenging, rewarding goals.
Upcoming Event: LPPDE NA 2022 In-Person Conference
October 3-6, 2022 in Newport, RI
Join us to learn how you can increase your innovation speed, eliminate waste in your processes, and lead your team to new levels of productivity and pride. Meet people like yourself who are striving for innovation excellence. Learn what works for them. Share your challenges and successes. We want to exchange ideas with you, so we all learn to innovate faster.
Hear keynote from Bruce Hamilton of GBMP on “Developing your Teams to Accelerate your LPPD Innovation.” Meet Durward Sobek, co-author of the book, Lean Product and Process Development. And many others with deep expertise in lean product development. See the full program at LPPDE NA 2022.